MIG/MAG welding consists in welding with an electric arc generated between the consumable electrode and the material being welded. The consumable electrode is a continuously fed wire. The arc and molten metal pool are protected by a stream of shielding gas.
Scheme of MIG/MAG welding
The welding wire flows smoothly from the holder and melts continuously in the electric arc. The molten wire material is mixed with the molten material to be bonded to form a liquid weld pool. After the arc moves away, the weld pool solidifies to form a permanent joint. Shielding gas is continuously supplied through the welding torch and its gas nozzle, which protects the molten metal against the atmosphere and cools the torch (additional liquid-cooled torches are also used).
The welding wire is supplied with voltage via a current cable coming from the power source (semi-automatic welding machine) and then transferred via a copper contact tip.
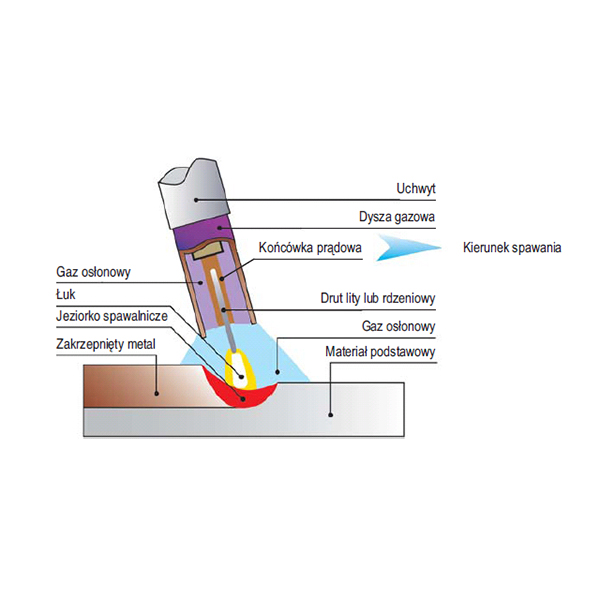

Pros
- universal method – various metals and their alloys can be welded in all positions,
- high welding efficiency – much higher than with coated electrodes,
- relatively low cost of welding materials – total costs lower by about 20% than the costs of welding with coated electrodes,
- good quality of welds,
- possibility to mechanize and automate the method.

Cons
- the quality of the welds depends largely on the skills of the welder,
- relatively high purchase costs of devices and equipment,
- MAG welding is more prone to sticking and porosity of the welds.